UV තීන්ත මුද්රණය සාමාන්යයෙන් ක්ෂණික UV වියලීමේ ක්රමය අනුගමනය කරයි, එවිට තීන්ත ඉක්මනින් චිත්රපට ස්වයං-ඇලවුම් ද්රව්යයේ මතුපිටට ඇලී සිටිය හැක. කෙසේ වෙතත්, මුද්රණ ක්රියාවලියේදී, චිත්රපට ස්වයං-ඇලවුම් ද්රව්ය මතුපිට UV තීන්තවල දුර්වල ඇලවීම පිළිබඳ ගැටළුව බොහෝ විට සිදු වේ.
පාරජම්බුල කිරණ තීන්තවල දුර්වල ඇලවීම කුමක්ද?
පාරජම්බුල කිරණ තීන්තවල දුර්වල ඇලවීම පරීක්ෂා කිරීම සඳහා විවිධ පර්යන්තවල විවිධ ක්රම තිබේ. කෙසේ වෙතත්, ස්වයං-ඇලවුම් ලේබල් කර්මාන්තයේ දී, බොහෝ පාරිභෝගිකයින් තීන්ත ඇලවුම් පරීක්ෂණය සඳහා 3M 810 හෝ 3M 610 ටේප් භාවිතා කරනු ඇත.
ඇගයීමේ නිර්ණායක: ඇලවුම් පටි ලේබලය මතුපිටට ඇලවීමෙන් පසුව ඉවත් කිරීමෙන් පසු ඇලවූ තීන්ත ප්රමාණය අනුව තීන්ත තද බව තක්සේරු කෙරේ.
1 මට්ටම: තීන්ත ගැලවී යන්නේ නැත
මට්ටම 2: තීන්ත ටිකක් වැටේ (<10%)
3 මට්ටම: මධ්යම තීන්ත වැගිරීම (10%~30%)
4 මට්ටම: බරපතල තීන්ත වැගිරීම (30%~60%)
5 මට්ටම: තීන්ත සියල්ලම පාහේ ගැලවී යයි (>60%)
ප්රශ්නය 1:
නිෂ්පාදනයේදී, සමහර ද්රව්ය සාමාන්ය ලෙස මුද්රණය කරන විට, තීන්ත ඇලවීම හරි, නමුත් මුද්රණ වේගය වැඩි දියුණු වූ පසු, තීන්ත ඇලවීම නරක අතට හැරෙන ගැටළුව අපට බොහෝ විට හමු වේ.
හේතුව1:
UV තීන්තයේ ඇති ෆොටෝඉනිටේටරය නිදහස් රැඩිකලුන් නිපදවීමට පාරජම්බුල කිරණ අවශෝෂණය කරන බැවින්, එය තීන්ත සංරචකයේ ඇති මොනෝමර් ප්රිපොලිමර් සමඟ සම්බන්ධ වී ජාල ව්යුහයක් සාදනු ඇත, එය ද්රවයේ සිට ඝන දක්වා තාවකාලික ක්රියාවලියකි. කෙසේ වෙතත්, සත්ය මුද්රණයේදී, තීන්ත මතුපිට ක්ෂණිකව වියළී ගියද, පාරජම්බුල කිරණවලට ඝන වූ තීන්ත මතුපිට ස්ථරයට විනිවිද යාමෙන් පහළ ස්ථරයට ළඟා වීමට අපහසු වූ අතර, එහි ප්රතිඵලයක් ලෙස පහළ ස්ථරයේ තීන්තවල අසම්පූර්ණ ප්රකාශ රසායනික ප්රතික්රියාවක් ඇති විය.
යෝජනාව:ගැඹුරු තීන්ත සහ සැහැල්ලු මුද්රණය සඳහා, තීන්ත තට්ටුවේ ඝණකම අඩු කිරීම සඳහා ඉහළ වර්ණ ශක්තිය තීන්ත භාවිතා කළ හැකි අතර, තනි ස්ථර තීන්තවල වියළි බව සහතික කිරීම පමණක් නොව, නිෂ්පාදන කාර්යක්ෂමතාව ඵලදායී ලෙස වැඩිදියුණු කළ හැකිය.
හේතුව2:
UV රසදිය ලාම්පුව සාමාන්යයෙන් පැය 1000ක් පමණ භාවිතා වන අතර UV ලාම්පුව පැය 1000කට වැඩි කාලයක් භාවිතා කිරීමෙන් පසුව එය දැල්විය හැකි නමුත් UV තීන්ත සම්පූර්ණයෙන්ම වියලීමට නොහැක. ඇත්ත වශයෙන්ම, UV ලාම්පුව එහි සේවා කාලය කරා ළඟා වූ පසු, එහි වර්ණාවලි වක්රය වෙනස් වී ඇත. විමෝචනය වන පාරජම්බුල කිරණ වියළි තීන්තවල අවශ්යතා සපුරාලන්නේ නැති අතර අධෝරක්ත ශක්තිය වැඩි වී ඇති අතර එහි ප්රතිඵලයක් ලෙස අධික උෂ්ණත්වය හේතුවෙන් ද්රව්ය විරූපණය සහ තීන්ත කැඩෙන සුළු වේ.
යෝජනාව:UV ලාම්පුව භාවිතා කරන කාලය නිවැරදිව සටහන් කර නියමිත වේලාවට ප්රතිස්ථාපනය කළ යුතුය. සාමාන්ය නිෂ්පාදනය අතරතුර, UV ලාම්පුවේ පිරිසිදුකම නිතිපතා පරීක්ෂා කිරීම සහ පරාවර්තකය පිරිසිදු කිරීම ද අවශ්ය වේ. සාමාන්යයෙන්, UV ලාම්පුවේ ශක්තියෙන් 1/3 ක් පමණක් ද්රව්ය මතුපිට සෘජුව බැබළෙන අතර ශක්තියෙන් 2/3 පරාවර්තකයෙන් පිළිබිඹු වේ.
ප්රශ්නය 2:
නිෂ්පාදනයේදී, සමහර ද්රව්ය සාමාන්ය ලෙස මුද්රණය කරන විට, තීන්ත ඇලවීම හරි, නමුත් මුද්රණ වේගය වැඩි දියුණු වූ පසු, තීන්ත ඇලවීම නරක අතට හැරෙන ගැටළුව අපට බොහෝ විට හමු වේ.
හේතුව 1:
තීන්ත සහ උපස්ථරය අතර කෙටි සම්බන්ධතා කාලය අංශු අතර ප්රමාණවත් අණුක මට්ටමේ සම්බන්ධතාවයකට මග පාදයි, ඇලීමට බලපායි.
තීන්ත සහ උපස්ථරයේ අංශු විසරණය වන අතර අණුක මට්ටමේ සම්බන්ධතාවයක් සෑදීමට එකිනෙකා සමඟ සම්බන්ධ වේ. වියළීමට පෙර තීන්ත සහ උපස්ථරය අතර සම්බන්ධතා කාලය වැඩි කිරීමෙන්, අණු අතර සම්බන්ධතා බලපෑම වඩාත් වැදගත් විය හැකි අතර එමඟින් තීන්ත ඇලවීම වැඩි වේ.
යෝජනාව: මුද්රණ වේගය අඩු කරන්න, තීන්ත උපස්ථරය සමඟ සම්පුර්ණයෙන්ම සම්බන්ධ කරන්න, සහ තීන්ත ඇලවීම වැඩි දියුණු කරන්න.
හේතුව 2:
UV ආලෝකයේ නිරාවරණ කාලය ප්රමාණවත් නොවීම, එහි ප්රතිඵලයක් ලෙස තීන්ත සම්පූර්ණයෙන්ම වියළී නොයෑම, ඇලීමට බලපායි
මුද්රණ වේගය වැඩිවීම නිසා UV ආලෝකයේ ප්රකිරණ කාලය ද කෙටි වන අතර එමඟින් තීන්ත මත බැබළෙන ශක්තිය අඩු වන අතර එමඟින් තීන්ත වියළන තත්ත්වයට බලපාන අතර අසම්පූර්ණ වියළීම හේතුවෙන් දුර්වල ඇලීම ඇති වේ.
යෝජනාව:මුද්රණ වේගය අඩු කරන්න, UV ආලෝකය යටතේ තීන්ත සම්පූර්ණයෙන්ම වියළීමට ඉඩ දෙන්න, සහ ඇලීම වැඩි දියුණු කරන්න.
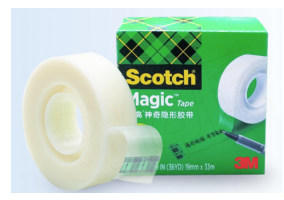
පසු කාලය: ඔක්තෝබර්-09-2022